فهرست مطالب
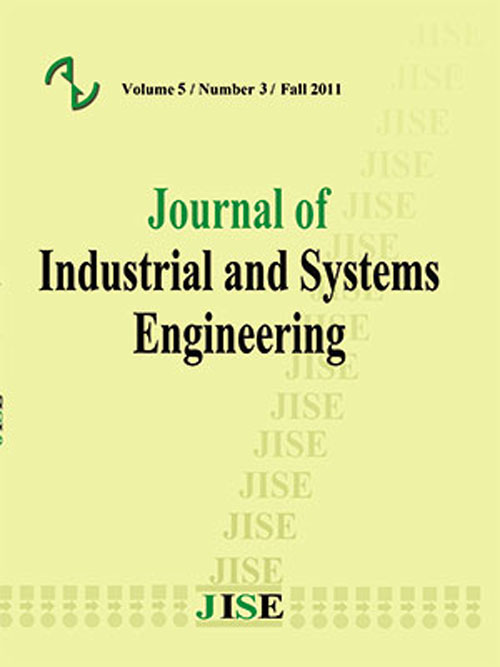
Journal of Industrial and Systems Engineering
Volume:10 Issue: 1, Winter 2017
- special issue on production and inventory
- تاریخ انتشار: 1396/02/25
- تعداد عناوین: 9
-
-
Pages 1-17In this article, manufacturer-retailer supply chain coordination (SCC) has been developed under periodic review inventory system. In the studied model, the retailer as downstream member uses periodic review inventory policy and decides about review period (T) and order-up-to-level (R). Also, the manufacturer as upstream member faces EPQ system and determines the number of shipments from manufacturer to retailer per production run (n) as a decision variable. Firstly, the problem is investigated in decentralized and centralized models and accordingly, in order to coordinate the mentioned supply chain, a coordination scheme based on quantity discount is proposed. Maximum and minimum discounts, which are acceptable for both members, are determined. Numerical examples and sensitivity analysis indicate that the proposed coordination scheme improves the profitability and performance of both members and entire SC toward decentralized model. Moreover, the developed coordination model can share extra profit between SC members according to their bargaining power fairly.Keywords: Manufacturer-retailer chain, periodic review inventory system, Production, supply chain coordination, Quantity discounts
-
Pages 18-29One of the primary assumptions in most optimal pricing methods is that the production cost is a non-increasing function of lot-size. This assumption does not hold for many real-world applications since the cost of unit production may have non-increasing trend up to a certain level and then it starts to increase for many reasons such as an increase in wages, depreciation, etc. Moreover, the production cost will eventually have a declining trend. This trend curve can be demonstrated in terms of cubic function and the resulted optimal pricing model can be modeled in Geometric Programming (GP). In this paper, we present a new optimal pricing model where the cost of production has different trends depending on the production size. The resulted problem is formulated as a parametric GP with five degrees of difficulty and it is solved using the recent advances of optimization techniques. The paper is supported with various numerical examples and the results are analyzed under different scenarios.Keywords: Geometric programming, Nonlinear Model, Production, Operations Management, Optimal pricing, Marketing planning
-
Pages 30-56One of the important aspects of distribution optimization problems is simultaneously, controlling the inventory while devising the best vehicle routing, which is a famous problem, called inventory-routing problem (IRP). When the lot-sizing decisions are jointed with IRP, the problem will get more complicated called production inventory-routing problem (PIRP). To become closer to the real life problems that includes products that have a limited life time like foods, it seems reasonable to narrow down the PIRP problem to the perishable products, which is perishable-production inventory-routing problem (P-PIRP). This paper addresses a P-PIRP in a two echelon supply chain system where the vendor must decide when and how much to produce and deliver products to the customers warehouse. Here, the general model of PIRP as mixed integer programming (MIP)is adopted and the perishability constraint are added in order to solve the P-PIRP problems. Due to the complexity of problem, providing solution for the medium to large instances cannot be easily achieved by business applications, and then using the meta-heuristics is unavoidable. The novelty of this research is devising an enhanced genetic algorithm (GA) using multiple repairing mechanisms, which because of its computationally cumbersomeness have absorbed less attention in the literature. The problem runs through some generated instances and shows superiority in comparison to the business application.Keywords: Production inventory routing problem, IRP, mixed integer-programming, perishable, Genetic Algorithm
-
Pages 57-72In this research, a single batch processing machine scheduling problem with minimization of total earliness and tardiness as the objective function is investigated.We first formulate the problem as a mixed integer linear programming model. Since the research problem is shown to be NP-hard, an improved memetic algorithmis proposed to efficiently solve the problem. To further enhance the memetic algorithm and avoid premature convergence, we hybridize it with a variable neighborhood search procedureas its local search engine. A dynamic programming approach is also proposed to find optimal schedule for a given set of batches. Wedesign a Taguchi experiment to evaluate the effects of different parameters on the performance of the proposed algorithm. The results of an extensive computational study demonstrate the efficacy of the proposed algorithm.Keywords: Batch processing machine, Total earliness, tardiness, Memetic algorithm, Variable neighborhood search, Dynamic programming
-
Pages 73-90One of the key elements in production planning hierarchy is master production scheduling. The aim of this study is to evaluate and compare thirteen alternative MPS development methods, including multi-objective optimization as well as twelve heuristics, in different operating conditions for multi-product single-level capacity-constrained production systems. We extract six critical criteria from the previous related researches and employ them in a MCDM framework. The Shannon entropy is used to weight the criterion and TOPSIS is proposed for ranking the alternative methods. To be able to generalize the results, 324 cases considering different operating conditions are simulated. The results show that the most important criteria are instability and inventory/setup costs, respectively. A performance analysis of MPS development methods is reported that the heuristics provides better results than multi-objective optimization in many conditions. A sensitivity analysis for critical parameters is also provided. Finally, the proposed methodology is implemented in a wire & cable company.Keywords: Master production scheduling, Multi-criteria decision making, heuristics, TOPSIS, Shannon entropy, Numerical simulation
-
Pages 91-108The basic assumption in the traditional inventory model is that all outputs are perfect items. However, this assumption is too simplistic in the most real-life situations due to a natural phenomenon in a production process. From this it is deduced that the system produces non-perfects items which can be classified into four groups of perfect, imperfect, reworkable defective and non-reworkable defective items. In this paper, compared with classic model, a new integrated imperfect quality economic production quantity problem is proposed where demand can be determined as a power function of selling price, advertising intensity, and customer services volume. Furthermore, as novelty way the unit cost is defined as a cubic function of outputs which is similar to real world. Also, a geometric programming modeling procedure is employed to formulate the problem. Finally, a numerical example is illustrated to study and analysis the behavior and application of the model.Keywords: Geometric programming, Inventory, Comprehensive demand function, Cubic production cost function, Non-perfect production process
-
Pages 109-131In this paper,a coordination model has been investigated for a two-level supply chain (SC) consisting of one retailer and one supplier under periodic review inventory system. The review period and the retailers safety factorare assumed to be decision variables. The retailer faces stochastic demand following a normal distribution with known mean and variance. Moreover, it is assumed that unmet demand will be backordered. Firstly, the investigated SC is modeled under the decentralized and centralized decision-making structures, afterwards, a coordination mechanism based on delay in payments is proposed for transition from the decentralized to centralized model. To fairly share the surplus profit obtained by coordination, a profit sharing strategy is developed which is based on the bargaining power of the two SC members. Finally, a set of numerical experiments and sensitivity analysis are carried out. Numerical examples indicate that the proposed delay in payments contract can achieve channel coordination and the whole SC cost will decrease under the coordination model while the costs of neither retailer nor the supplier will increase.Keywords: supply chain coordination, periodic review inventory system, delay in payments, profit sharing
-
Pages 132-154Scheduling for a two-stage production system is one of the most common problems in production management. In this production system, a number of products are produced and each product is assembled from a set of parts. The parts are produced in the first stage that is a fabrication stage and then they are assembled in the second stage that usually is an assembly stage. In this article, the first stage assumed as a hybrid flow shop with identical parallel machines and the second stage will be an assembling work station. Two objective functions are considered that are minimizing the makespan and minimizing the sum of earliness and tardiness of products. At first, the problem is defined and its mathematical model is presented. Since the considered problem is NP-hard, the multi-objective genetic algorithm (MOGA) is used to solve this problem in two phases. In the first phase the sequence of the products assembly is determined and in the second phase, the parts of each product are scheduled to be fabricated. In each iteration of the proposed algorithm, the new population is selected based on the non-dominance rule and fitness value. To validate the performance of the proposed algorithm, in terms of solution quality and diversity level, various test problems are designed and the reliability of the proposed algorithm is compared with two prominent multi-objective genetic algorithms, i.e. WBGA, and NSGA-II. The computational results show that the performance of the proposed algorithms is good in both efficiency and effectiveness criteria. In small-sized problems, the number of non-dominance solution come out from the two algorithms N-WBGA (the proposed algorithm) and NSGA-II is approximately equal. Also, more than 90% solution of algorithms N-WBGA and NSGA-II are identical to the Pareto-optimal result. Also in medium problems, two algorithms N-WBGA and NSGA-II have approximately an equal performance and both of them are better than WBGA. But in large-sized problems, N-WBGA presents the best results in all indicators.Keywords: Multi-objective Genetic algorithm, Two-stage production system, Assembly
-
Solving a multi-objective mixed-model assembly line balancing and sequencing problemPages 155-170This research addresses the mixed-model assembly line (MMAL) by considering various constraints. In MMALs, several types of products which their similarity is so high are made on an assembly line. As a consequence, it is possible to assemble and make several types of products simultaneously without spending any additional time. The proposed multi-objective model considers the balancing and sequencing problems, simultaneously. Based on the assembly problem, the various tasks of models are assigned to the workstations, while in the sequencing problem, a sequence of models for production is determined. The two meta-heuristic algorithms, namely MOPSO and NSGA-II are used to solve the developed model and different comparison metrics are applied to compare these two proposed meta-heuristics. Several test problems based on empirical data is used to illustrate the performance of our proposed model. The results show that NSGA-II outperforms the MOPSO algorithm in most metrics used in this paper. Moreover, the results indicate that our proposed model is more effective and efficient to assignment of tasks and sequencing models than manual strategy. Finally, conclusion remarks and future research are provided.Keywords: mixed-model assembly line, sequencing, balancing, mixed-integer linear programming, meta-heuristic algorithms